The person in charge
prof. Janusz Kozak,
Location
I and II floor, building No 30 in University Campus.
Office
Dorota Okoń MSc, ME
building IOiO (30) room 121
phone +48 58 347 17 93 , +48 58 347 15 48
dokon@pg.edu.pl
Research profile
From very beginning research area of chair workers has been focused on problems of manufacturing and maintenance of floating objects. Detailed description of research profile – in bookmark.
Department collaborates in commercial level with shipbuilding sector companies as well as with some other market enterprises.
Educational Profile
As baseline educational profile, the chair gives lectures on technology of ship manufacturing and repair technology, problems of outfitting as well as problems of economy and management of production. We teach also manufacturing techniques like welding, materials as well as relations of manufacturing quality and the matters of strength of materials and structures. On MSc course we give lectures on problems of ship structure failure, exploitation strength, role of Classification Societies, global shipping market analysis, project management and introduction to quality systems in industry. Into study program we included problems of modern material and technologies like laser welding and application of steel, laser welded sandwich panels into ship structure. Starting from 2004 the Department has been carrying out post diploma studies ISO Standards and TQM (in polish).
Laboratory of Marine Structures
Laboratory occupies area of 600 m2

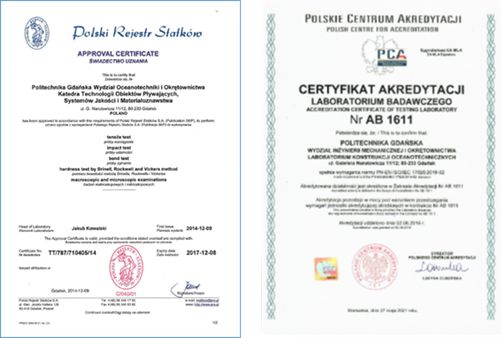
Basic equipment
- Experimental stand for static and fatigue investigations of full-sized structural elements or ship hull structure models dimensions of up to 17 m x 7 m. The instrumentation of this stand consists of steel frames of 7 m and 5 m span respectively, allowing different supporting, fixing and loading of the tested structures with complex modes of the boundary conditions. Each frame can carry the static and dynamic forces up to 5000 kN and 2000 kN in vertical and horizontal directions respectively. Load is generated by set of hydraulic actuators with capabilities up to 1000 kN each, which can be coupled to create different combinations – controlled by system Instron-LABTRONIC 8800 with possibility of generating of different type and range of static and fatigue load in four channel simultaneously.
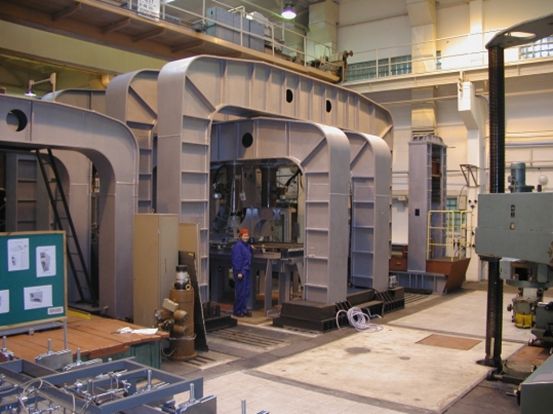
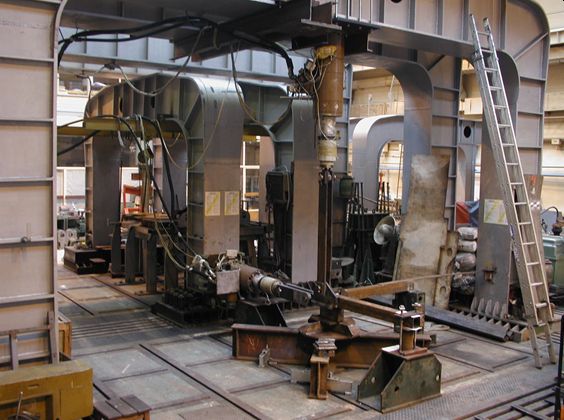
Versatile testing machine for static and fatigue tests of structural members;
The main features of the testing machine are:
- compression – up to 2000 kN
- tension – up to 4000 kN
- fatigue load of the amplitude up to 1200 kN and frequency to 10 Hz
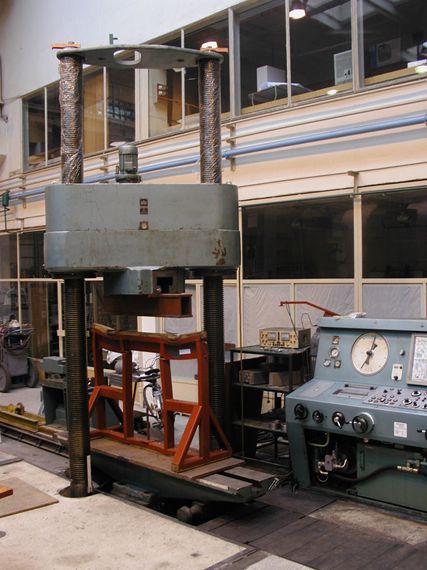
- Instron 8600 series strength machine with capacity ±500 kN (static and fatigue)
- MTS 809.10 biaxial strength machine, with strength capacity ±100 kN and moment capacity ±1100 Nm. Machine is equipped with environmental chamber with operational temperature range from -129°C to 540°C.
- Some specialised stands for static, fatigue and impact tests under mixed load configuration:
- Versatile testing machine for static and fatigue tests of specimen or small size structural members: static compression and tension – up to 400 kN, fatigue load of the amplitude up to 250 kN and frequency to 10 Hz,
- Versatile testing machine for static and fatigue tests of specimen or small size structural members: static compression and tension – up to 250 kN, fatigue load of the amplitude up to 200 kN and frequency to 10 Hz,
- Versatile testing machine for standard static tests of specimen: compression and tension – up to 100 kN,
- Charpy pendulum machine,
- Drop test machine (up to 7 m drop weight height, up to 50 kg dropped mass),
- Measurement and data acquisition devices:
-
- QuantumX system which can operate separately or in synchronised cluster:
- 1x HBM QuantumX MX840A - 8 channel amplifier quarter, half and full bridge configuration for strain gauges, current signals and resistance.
- 2x HBM QuantumX MX1615B - 16 channel amplifier quarter, half and full bridge configuration for strain gauges, current signals and resistance.
- 1x QuantumX MX1609 - 16 channel amplifier for T-type thermocouple
- 1x QuantumX CX22 - data acquisition module
- Software CatmanEasy in 5.1.x version for data acquisition and analysis of registered data.
- GOM Aramis SRX Digital Image Correlation System
- QuantumX system which can operate separately or in synchronised cluster:
-
- Metallographic laboratory equipped with hardness and micro hardness measuring apparatus, optical metallographic microscope and electronic microscopes of and TEM types.
- SEM BS 301 TESLA with digital picture registration system SAD 181,
- Digital microscope 3D Keyence VHX 7000
- Other utilities: heavy assembling shop for production of bulky structures (equipment: crane 12,5 t, stands for manual, half-automatic and automatic welding, plasma equipment for cutting up to 30 mm thickness, specialised torches for no hammering straightening of steel and aluminum alloy structures.
Selected publications
- Kozak J.: Joints Of Steel Sandwich Structures// Polish Maritime Research -Vol. 28,iss. 2 (2021), s.128-135, 10.2478/pomr-2021-0029
- Wołoszyk K., Garbatov Y., Kowalski J.: Indoor accelerated controlled corrosion degradation test of small- and large-scale specimens// OCEAN ENGINEERING -,iss. 241 (2021), s.110039-
- Kowalski J.: EXPERIMENTAL AND NUMERICAL INVESTIGATION ON SPECIMEN GEOMETRY EFFECT ON THE CTOD VALUE FOR VL-E36 SHIPBUILDING STEEL// Polish Maritime Research -Vol. 28,iss. 3 (2021), s.110-116
- Wołoszyk K., Garbatov Y., Kowalski J., Samson L.: Numerical and experimental study on effect of boundary conditions during testing of stiffened plates subjected to compressive loads// ENGINEERING STRUCTURES -Vol. 235, (2021),
- Niklas, K., & Bera, A. (2021). The influence of selected strain-based failure criteria on ship structure damage resulting from a collision with an offshore wind turbine monopile. Polish Maritime Research, 28, 42-52. https://doi.org/10.2478/pomr-2021-0048
- Niklas, K., & Karczewski, A. (2020). Determination of seakeeping performance for a case study vessel by the strip theory method. Polish Maritime Research, 27, 4-16. https://doi.org/10.2478/pomr-2020-0061,
- Kowalski J., Licznerski Ł., Supernak-Marczewska M., Emilianowicz K.: Influence of process of straightening ship hull structure made of 316L stainless steel on corrosion resistance and mechanical properties// Polish Maritime Research -Vol. 27,iss. 4 (108) (2020), s.103-111
- Wołoszyk K., Garbatov Y., Kowalski J., Samson L.: Experimental and numerical investigations of ultimate strength of imperfect stiffened plates of different slenderness// Polish Maritime Research -Vol. 27,iss. 4(108) (2020), s.120-129
- Kowalski J., Supernak-Marczewska M., Emilianowicz K., Nadolny L.: Wpływ błędów technologicznych na degradację korozyjną stopu miedzi z grupy cunifer – CuNi10Fe1,6Mn// Mechanik. -., iss. 5-6 (2019), s.391-394,
- Niklas, K. (2014). Calculations of notch stress factor of a thin-walled spreader bracket fillet weld with the use of a local stress approach. ENGINEERING FAILURE ANALYSIS, 45, 326-338. https://doi.org/10.1016/j.engfailanal.2014.06.017,
- Niklas, K., & Kozak, J. (2016). Experimental investigation of Steel–Concrete–Polymer composite barrier for the ship internal tank construction. OCEAN ENGINEERING, 111, 449-460. https://doi.org/10.1016/j.oceaneng.2015.11.030,
- Niklas, K. (2017). Strength analysis of a large-size supporting structure for an offshore wind turbine. Polish Maritime Research, 24(S1 (93), 156-165. https://doi.org/10.1515/pomr-2017-0034,
- Niklas, K., & Kozak, J. (2018). The effect of numerical 2D and 3D FEM element modelling on strain and stress distributions at laser weld notches in steel sandwich type panels. Polish Maritime Research, 25(1(97), 121-127. https://doi.org/10.2478/pomr-2018-0014,
- Ringsberg, J., Amdahl, J., Chen, B., Cho, S.-R., Ehlers, S., Hu, Z., Kubiczek, J., Kõrgesaar, M., Liu, B., Marinatos, J., Niklas, K., Parunov, J., Quinton, B., Rudan, S., Samuelides, M., Soares, C., Tabri, K., Villavicencio, R., Yamada, Y., Yu, Z., & Zhang, S. (2018). MARSTRUCT benchmark study on nonlinear FE simulation of an experiment of an indenter impact with a ship side-shell structure. MARINE STRUCTURES, 59, 142-157. https://doi.org/10.1016/j.marstruc.2018.01.010,
- Niklas, K., & Pruszko, H. (2019). Full-scale CFD simulations for the determination of ship resistance as a rational, alternative method to towing tank experiments. OCEAN ENGINEERING, 190. https://doi.org/10.1016/j.oceaneng.2019.106435, 140 pkt.
- Niklas, K., & Pruszko, H. (2019). Full scale CFD seakeeping simulations for case study ship redesigned from V-shaped bulbous bow to X-bow hull form. APPLIED OCEAN RESEARCH, 89, 188-201. https://doi.org/10.1016/j.apor.2019.05.011, 100 pkt.
- Litwin, W., Leśniewski, W., Piątek, D., & Niklas, K. (2019). Experimental Research on the Energy Efficiency of a Parallel Hybrid Drive for an Inland Ship. ENERGIES, 12, 1-16, https://doi.org/10.3390/en12091675, 140 pkt.
Selected research projects
- Novel design of overhead high tension line tower, (POIR.04.01.04-00-0060/20), NCBiR, 2021-2022
- Design of algorithm as well as methodology for design process of JACKET type supporting structure for offshore transformer station, POIR, NCBiR, 2021 - 2023
- SmartPS – „Smart Propulsion Systems“, ERA-NET MARTECII/SmartPS/4/2016, 2017-2019