Research and development activities:
- Weldability of steel in underwater conditions
- Studies of friction stir welding (FSW) processes
- Research on environmental embrittlement of metals and their welded joints
- Corrosion tests of metals and welded joints
- Weldability assessment
- Influence of diffusible hydrogen content in deposited metal on the mechanical properties of welded joints
- Explosive welding process
- Multidimensional analyzes in welding engineering
- Basic research in the field of: theory of thermal processes in welding, theory of welding stresses and deformations, brittle and delayed cracks, theoretical foundations and technologies of explosive welding
- Computer-aided design of welding technology
- Non-destructive tests of welded structures and casts by visual test (VT), penetrant test (PT), magnetic particle test (MT), radiographic test (RT), traditional ultrasonic test (UT), TOFD and Phassed Array
- Design of welding processes
- Automation and robotization of welding processes
- Design of welded structures made of corrosion-resistant steels
- Design and production of fibrous composites with a polymer matrix modified with nanoparticles
- Design and production of surface layers with increased resistance to influence of the aquatic environment (also modification with nanoparticles)
- Expertise opinions on damage of metal materials and welded structures
- Degradation assessment of materials working at high temperatures
- Determining the mechanical properties of engineering materials, especially welded joints:
- Tensile strength tests
- Hardness measurements
- Metallographic tests
- Charpy impact tests – also at lower temperatures (-20 i -40°C)
- Environmental aging in a climatic chamber (180°C / -40°C) with adjustable humidity
- Corrosion resistance tests of metals and welded joints:
- Slow Strain Rate Tensile tests
- Constant Load tests
- Assessment of diffusible hydrogen content in deposited metal
- Impact resistance tests with the use of an INSTRON CEAST 9130 drop hammer
- Determining the susceptibility to cold cracking on the basis of technological tests and the implant test
- Qualification of welding technology, also in underwater conditions
- Certification of divers-welders in accordance with PN-EN ISO and AWS standards
- Quality supervision of welded structures
- Expertise opinions and consulting of welding technologies of structires by EN ISO, ASME, AWS requirements
- Regeneration technologies of machine elements
Training offer:
Postgraduate studies - International Welding Engineer IWE I, IWE II, IWE III Authorized Training Center of the International Institute of Welding.
Apparatus available at the Department laboratories:
- SAW welding device ESAB A2 Multitrac + welding power source 1000A
- MIG/MAG + MMA ESAB Aristo Mig 4004 Pulse device
- TIG AC-DC ESAB Caddy Tig 2200i device
- Plasma cutting and gouging device ESAB PowerCut 1600
- Devices for resistance (spot and butt) welding, friction welding and friction stir welding (FSW) also in water environment
- Fiber laser for welding IPG – YLS-6000 with Fanuc M710 robot
- Defectoscopes OMNISCAN MX: OLYMPUS, EPOCH1000i (GE - OLYMPUS), PHASOR XS (Krautkramer)
- Radiographic chamber, RTG Picker Andrex 3001 (300kV) aparatus
- Stands for testing stress corrosion cracking (SSRT, CL)
- Bruker diffusible hudrogen content measurement stand
- Resistance furnace for heat treatment
- Metal forming devices:
- hydraulic press,
- mechanical press,
- cutting stand,
- roll forming device,
- drawing device.
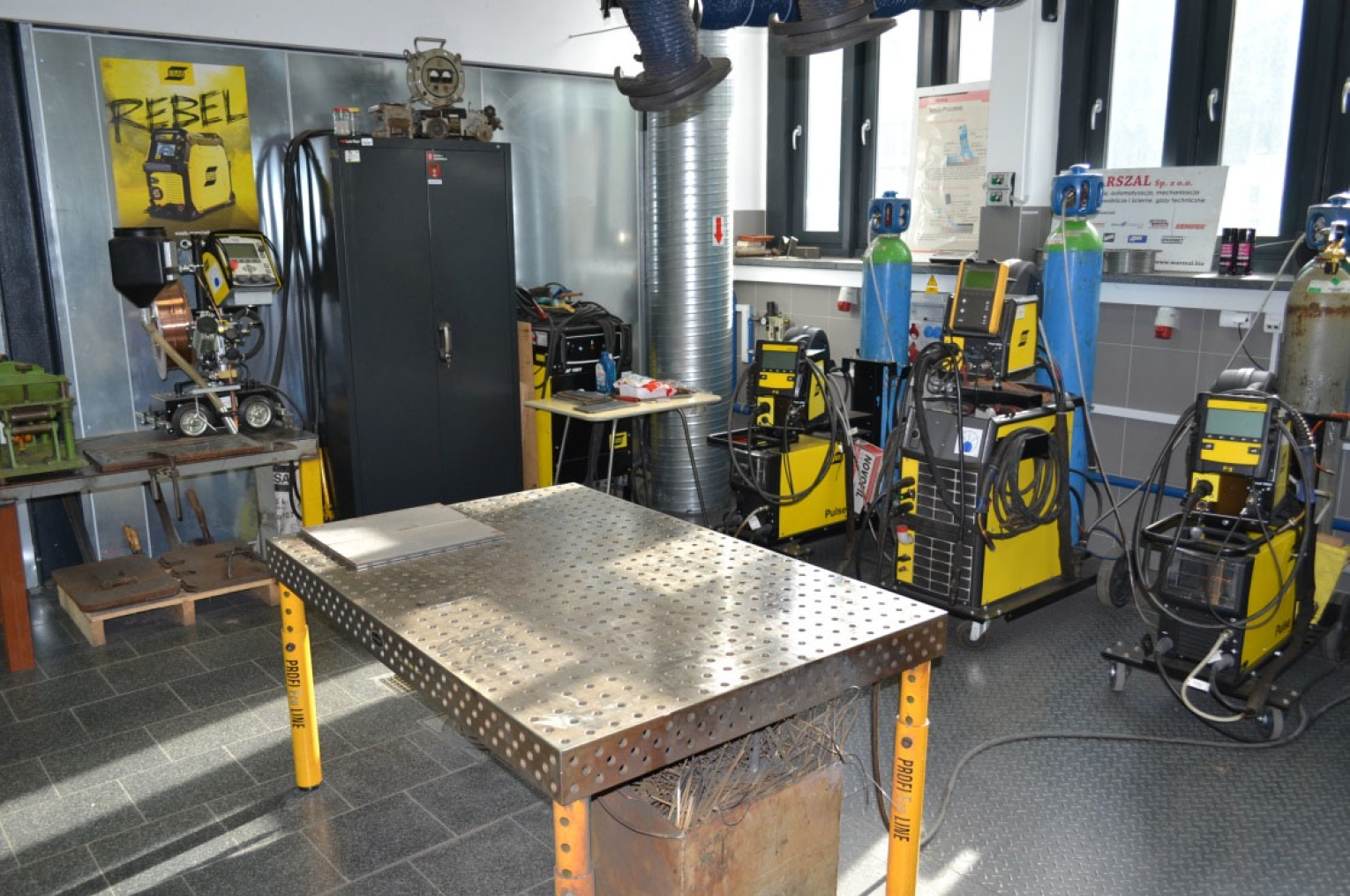
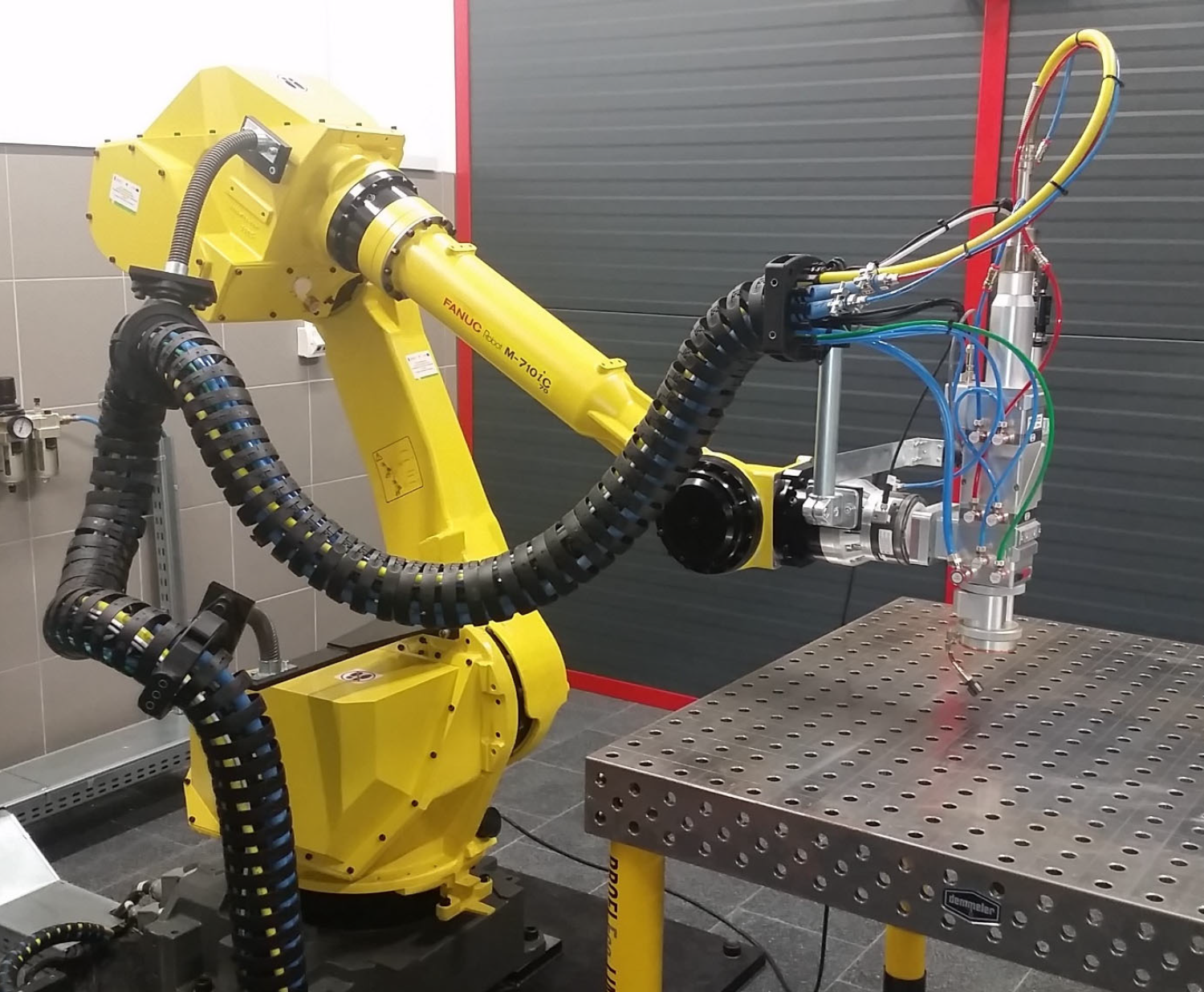
Cooperation with companies:
NST, Kobelco, Lincoln Electric, Kemppi, Esab, Marszal, Figel, Messer, Linde, Nauta Shipyard, Crist Shipyard, Gdańsk Shipyard, Lotos, TTU, Hexonic, Polmor
Exemplary scientific publications:
- Świerczyńska A., Fydrych D., Rogalski G.: Diffusible hydrogen managment in underwater wet self-shielded flux cored arc welding. International Journal of Hydrogen Energy, 2017, 42(38), 24532-24540.
- Tomków J., Rogalski G., Fydrych D., Łabanowski J.: Improvement of S355G10+N steel weldability in water environment by Temper Bead Welding. Journal of Materials Processing Technology, 2018, 262, 372-381.
- Świerczyńska A., Fydrych D., Landowski M., Rogalski G., Łabanowski J.: Hydrogen embrittlement of X2CrNiMoCuN25-6-3 super duplex stainless steel welded joints under cathodic protection. Construction and Building Materials, 2020, 238, 117697.
- Tomków J., Fydrych D., Rogalski G.: Dissimilar underwater wet welding of HSLA steels. The International Journal of Advanced Manufacturing Technology, 2020, 109, 717-725.
- Tomków J., Landowski M., Fydrych D., Rogalski G.: Underwater wet welding of S1300 ultra-high strength steel. Marine Structures, 2022, 81, 103120.