Journal bearings’ fatigue tester with revolving load vector
MWO - test rig for experimental evaluation of endurance limit of the dynamically loaded thin walled journal bearing shells with sheet metal backing and polymetallic lining. The machine can also perform tests with rolling element bearings as fatigue simulator or bearing noise testing environment.
MWO test stand is a machine with rotating load vector for investigating fatigue strength of plain bearing surface layer.
A pair of tested bearings (1) housed in the supports (4) are run simultaneously. Bearing loading is developed as a centrifugal force coming from the controlled dynamic unbalancing of the shaft (2) by dead weights (3). Bearing housings are attached to a stabilising bar (6) supported on a ball pivot (8) and four elastic supports (7). Bearings are fed with lubricating oil through a system of holes inside the shaft. Owing to load rotation, cyclic stress pulse travels over the entire circumference of the shell with every turn. The stress comprises compressive, radial stresses and variable tangential stress that alternates from tension to compression.
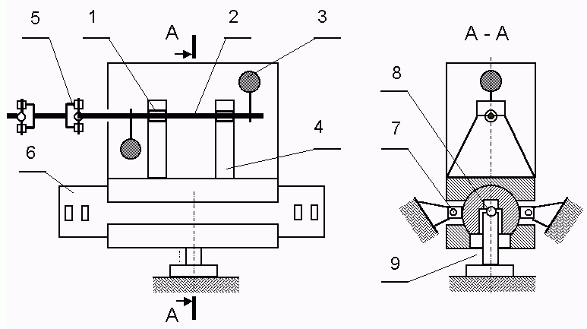
- tested bearing
- shaft
- loading masses
- bearing support
- Cardan universal joint
- seismic mass
- pivoted elastic support
- ball-and-socket rocker joint
- spring with travel limiter
The test rig, general view
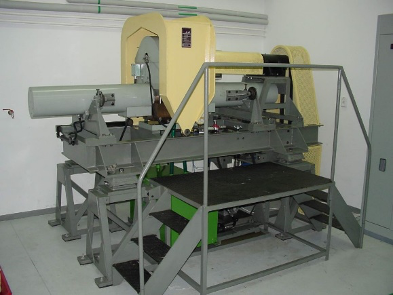
The test head
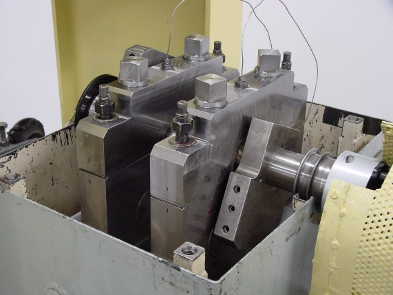
Specifications
- Maximum rotary bearing reaction: 120kN
- Maximum specific load: 128 MPa
- Shaft rotational speed: 300 - 4500 rpm
- Diameter of standard journal: 52.700 mm
- Width of standard bush: up to 50 mm
- Fatigue test sequence according to two-point strategy
Measured and controlled parameters
- Magnitude of load
- Number of load cycles
- Shaft rotational speed
- Bearing temperature
- Feed pressure of lubricating oil
- Oil temperature
- Intensity of oil flow
Contact person
- Michał Wasilczuk mwasilcz@pg.edu.pl
- Jacek Łubiński jacek.lubinski@pg.edu.pl